GENERAL PROCEDURE
Non-printed pouches:
Step One: Material Structure
The right material structure for packaging your product is based on several factors. We work together to find the best solution using these criteria:
Type of product. What are you packaging, and what properties does it have? Is it a powder, liquid, sharp, heavy, greasy, oily, etc.?
Visibility. Do you want to be able to see your product completely, have a clear window for some visibility, or should your packaging be completely opaque?
Weight. How much of your product will go into each pouch? Sample weights include 150 grams, 1 pound, 5 pounds, etc.
Style. What style of stand up pouch do you prefer? Options include flat barrier bags, flat bottom bags, spouted pouches for liquids, rollstock, and more.Features. Do you need special features like hang holes, tear notches, zippers, gas release valves, resealability, or other functionality?
Conditions. What kind of conditions will your packaged product be subjected to throughout your supply chain? Does your pouch need to withstand heat, high risk of puncture, rough handling, or other potentially damaging environments?
Step Two: Size
Once you’ve determined the material structure for your packaging, you need to define the relative size of your pouch. It can be challenging to know what the best size is for your product, but we’re here to help. Your MTPACK project manager will work with you to answer any questions and help choose from our variety of stock and custom sizes.
Step Three: Artwork
When you’ve chosen the right material and size for your stand up pouch, it’s time for design. You can provide completed artwork for us to use, or work with our graphic design team to create the perfect look for your product. Here’s what we’ll need when you submit your final design:
Multiple copies of your artwork:
o 2 hard color copies, 1 hard black and white copy
o 3 digital versions in Adobe Illustrator or Photoshop file format:
1 EPS copy converted into outline
1 EPS copy unconverted
1 PDF
A copy of your true color standards (PMS numbers or color samples) so your colors can be matched identically.
Outlines around all of the text in your printed stand up pouch design. Outlines turn text into small graphic designs, so your fonts won’t be distorted in the translation process.
All of the individual images used in your design with a resolution of at least 350 dpi. Make sure not to flatten your image layers.
The UPC.
Step Four: Manufacturing
You’ve chosen the material, size, and design that will best showcase your product. Time to manufacture your packaging!
Normal lead time for custom printed stand up pouches is 4 weeks after artwork approval. Here’s how that breaks down:
Week 1: Printing cylinders are created. Each of the colors in your final artwork requires a printing cylinder. Once the cylinders are created, the plant will ink them up and make a basic film proof.
Weeks 2 and 3: The inner liners are printed and the layers are run.
Weeks 3 and 4: The layers are laminated together and converted into the finished pouch size. Any extra features are applied, and your pouches are complete!
Step Five: Shipping and Payment
Shipping: Mostly FOB term(ship to your nearest port) , you can let us know.
Payment:
100% down on cylinders at time of order
50% down on pouches once the film proofs are approved
Balance will be paid before shipping
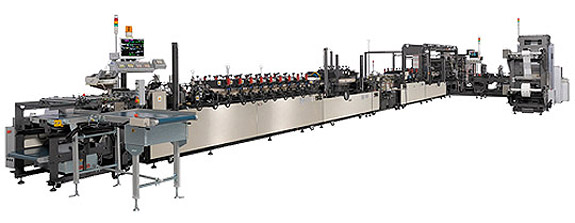
flexible packaging, retort pouch, flat bottom pouch, stand up pouch, spout pouch, rollstock